Building Input Costs & Margins For International Modular Homes Builder
Who: Large Modular House Builder
Where: Domestic factory and operations, with units shipped internationally to New Zealand and Fiji
Challenge: Decreasing margins, increasing materials and input costs
Solution: Precise, accurate analysis of various production cost bases and budgets
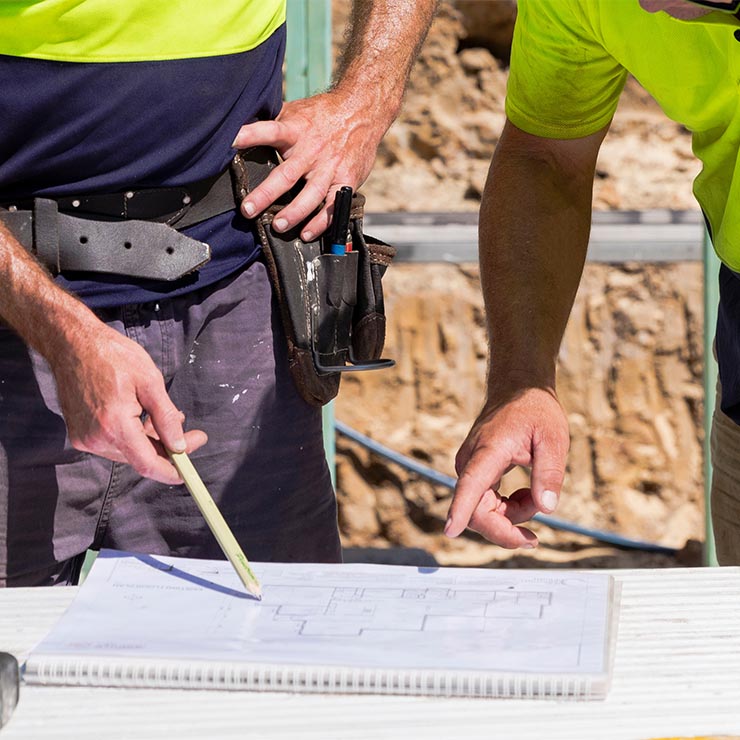
Client Requirements
Fed up with declining margins during the peak of building material prices in 2021 and 2022, this Modular Builder contacted Vision BI to find an easy, accurate way of identifying where their margins were being eroded across multiple jobs.
After establishing the client’s wish list of data analysis outcomes, our industry experts evaluated the business scope and systems currently in place. Vision BI then laid out a blueprint for the dashboard that would help provide insight to their business. We then harvested the data using SQL and a data pipeline, which allowed us to provide the client with live and visual data analysis.
The design Vision BI created enabled this client to access data from their accounting system, project management system and their CRM all in one user-friendly, low maintenance dashboard.
Vision BI was then able to provide ongoing support, in the form of monthly CFO advisory meetings, ensuring our client’s business was supported throughout their expansion by our skilled team.
Outcomes
From the client's initial request it took us only 4 weeks to go live with a dashboard, and best of all they required no internal resources or time allocation to do this!
The client was able to visualise key data across over 200 of their live active projects
Vision BI’s dashboard provided insight and trend analysis into the common areas margins and budgets that were being eroded
The client was able to identify opportunities to reduce costs and boost margins through material variations, and through performance management of staff